Projeto GASTAU
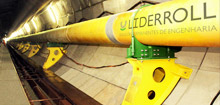
Projetado para escoar a produção de gás natural no campo de Mexilhão, na cidade de Caraguatatuba, litoral norte de São Paulo com extensão de 96 km e com capacidade para transportar 15 milhões de m³/dia, o gasoduto Caraguatatuba-Taubaté (GASTAU) figura como uma das obras de dutos que envolveu a maior sinergia entre as diversas áreas tecnológicas e empresas de engenharia nacionais e internacionais, tornando-se a obra mais emblemática da Petrobras na atualidade.
Além de sua importância para o abastecimento do mercado e para o setor energético do país, o projeto também se destaca pelos desafios de sua execução, os quais impuseram diversos obstáculos e necessidade de superação por todas as empresas convidadas pela Petrobras a participarem do projeto.
Entre eles, escoar o gás natural da unidade de Caraguatatuba por meio de um duto construído dentro de um túnel de 5.120 metros de extensão, por 5.2 metros de diâmetro, possuindo somente uma entrada (emboque) e sem saída na outra extremidade, possuindo paredes circulares, ventilação forçada e uma pista de rodagem de apenas 2.3 metros de largura, o que dificultava e restringia radicalmente a circulação dos técnicos, dos equipamentos de montagem e das próprias locomotivas e funcionários da empresa responsável pela escavação do túnel.
Foi um projeto de grande complexidade. A obra que, segundo a direção da PETROBRAS, tem papel estratégico no avanço de desenvolvimento do pré-sal na bacia de Santos, exigiu a superação de uma série de desafios técnicos por parte das equipes de projeto, engenharia e construção da LIDERROLL, uma vez que a montagem dos suportes, dos roletes motrizes e a operação de lançamento do Gasoduto se deram ao mesmo tempo em que a parte civil do túnel ainda estava sendo escavada por outra empresa, ou seja, tivemos que projetar tudo de forma a permitir trabalharmos instalando a nossa tecnologia e operando a nossa nova metodologia com várias empresas e equipes também trabalhando e circulando dentro do túnel.
A adoção e utilização da “faixa de duto” por dentro de um túnel foi decidida para reduzir imensos impactos ambientais, tais como o desmatamento de extensas áreas na Serra do Mar, a preservação quanto à destruição da fauna e flora local, bem como eliminar os riscos humanos das difíceis transposições da topografia da própria serra, o que comprovou a capacidade de gerenciamento da Petrobras e sua responsabilidade com o meio ambiente.
Em função disto, a PETROBRAS, por saber da imensa dificuldade do transporte dos tubos para o interior do túnel (operação de desfile), uma vez que os guindastes não conseguiriam entrar no mesmo, no interior do túnel não existiria um local para sua armazenagem (na parede circular seria impossível e no piso bloquearia todo e qualquer trânsito) e por reconhecer os riscos de intoxicações respiratórias em função dos gases gerados pelo processo de soldagem dos tubos e do possível comprometimento da qualidade dos serviços, bem como que os prazos seriam longos e incompatíveis com o cronograma de produção, corroborado ainda com a alta probabilidade de acidentes, a Petrobras solicitou que a LIDERROLL fizesse o desenvolvimento de uma tecnologia e processo, o qual eliminassem todos os riscos, mas atendessem as exigências necessárias para o lançamento da coluna de 5.100 metros pela parede circular do túnel e sem nenhuma atividade de solda dentro do mesmo.
No momento que a LIDERROLL foi consultada pela PETROBRAS e teve conhecimento do projeto original desenvolvido pela engenharia da Petrobras, o qual seria fabricado e instalado no interior do túnel, nosso departamento de projeto, em conjunto com o departamento de planejamento de obras, detectaram o elevado custo da estrutura projetada pela PETROBRAS, a dificulade logística do transporte das partes e peças para o interior do túnel, a dificuldade de se prover energia elétrica e etc, bem como o comprometimento da qualidade dos serviços (soldas, inspeçoes e pinturas), aliado ao prazo muito grande para o transporte, montagem e liberação das estruturas. Somou-se a isto o custo e a demora no desfile dos tubos no interior do túnel (gindastes não entrariam no túnel) e com isso seria uma operação perigosa e lenta, e por fim, os riscos de vida e a alta insalubridade gerada pelos gases liberados pelo processo de soldagem dentro do ambiente confinado ( túnel).
A LIDERROLL resolveu quebrar o paradigma e mudar o conceito tradicional construtivo de dutos utilizado em todo o mundo, que é o de se transportar, desfilar os tubos na faixa, alinhá-los e depois vir com as frentes de trabalho (Guindastes; Soldadores, Lixadores, Geradores, Inspetores, Pintura, Fiscalização, Banheiros, Posto médico, Refeitório e etc) avançando para frente do duto e, neste caso, para dentro do ambiente cada vez mais confinado por nao ter saída na outra extremidade do túnel.
A nossa metodologia inovou e quebrou esta lógica natural quando inverteu as referências e primou por manter todo estes profissinais e toda a logistica, do lado de fora do túnel (na entrada) com 01 pipeshop FIXO onde tudo ficaria organizado e com fácil acesso, bem como com alto graú de segurança, sem riscos ao meio ambiente e aos funiconários. Para isso quem deveria se mover em relação a todos e a tudo, deveria ser o Gasoduto.
Considerando agora essa premissa, começamos por projetar todos os suportes de forma modular® ojetivando supotar vários Roletes Motrizes especiais(RPAP)® e todo sistema elétrico tipo plugin que permitisse uma montagem independente do nosso sistema.
Com essa fiklosofia construtiva, foi obtida uma redução de aproximadamente 80% dos prazos de instalação comparado com o projeto original. Diminuimos consideradamente os custos (tendo em vista que só foi preciso instalar esta estrutura singela para um único duto; ao invés de ter que se construir toda uma estrutura complexa e completamente ancorada no teto e com soldas em insertes metálicos nas paredes para ficar estável e equilibrada – Com isso aumentamos ao máximo a segurança operacional (não houve, sequer, um único acidente ou intoxicação por gases de soldas, mesmo com a circulação das composições dos trens da construção civil do túnel).
A velocidade,a qualidade das soldas, os relatórios das inspeções e o Boletim de Avaliação e Desempenho (BAD) da PETROBRAS, registram a qualidade do nosso sistema e o desempenho da LIDERROLL, pois nossas notas foram 100 (nota máxima) em todos os itens, as quais atestam e comprovam os ganhos, as vantagens e a segurança da aplicação do novo processo construtivo e da tecnologia desevolvida pela LIDERROLL.
A LIDERROLL, precisava lançar um Gasoduto com deslocamento autônomo e movimento contínuo, obedecendo o sentido do seu eixo axial e 100% na posição horizontal para dentro de um túnel com 5.100 metros de comprimento e sendo o gasoduto de 28 polegadas de diâmetro X 0,625” de espessura. Este gasoduto teria que ser lançado e fixado na parede circular do túnel com 5.120 metros de comprimento e 5,2 metros de diâmetro, tendo um piso de somente 2,3 metros de área plana por onde poderia circular veículos leves e uma inclinação de subida de 3%, onde somente Pick-ups poderiam trafegar. Uma sempre no sentido de entrada e outra sempre no sentido da saída.
Cada tubo pesava 3,5 toneladas e a cada 12 metros teria que ser feito um solda circunferencial para emendá-los de forma a compor o Gasoduto. Como a área de trabalho e o piso do túnel eram muito apertados, quase nenhuma logística era possível e desta forma nenhum tipo de guindaste ou caminhão poderia levar os tubos para dentro do túnel. Outro fator de dificuldade era que a seção do túnel era circular, onde os tubos se levados para dentro do túnel teriam que ficar no piso, e ai sim, qualquer logistica ou deslocamento de pessoal e pick-ups não mais poderia ser feito.
Aliado a isto, o túnel possuia um complicador ainda maior, uma vez que nao existia saída na outra extremidade (tratava-se de uma galeria), e desta forma não existia áreas de manobra ou possbilidade de recursos ou frentes de trabalho disponíveis na outra extremidade. As temperaturas e umidade eram muito altas devida a falta de circulação de ar e toda potência elétrica, pessoal e logística ao longo dos 5.120 metros deveria ser providas por um único lado, a entrada.
Outro ponto de grande dificuldade era que as paredes circulares do tunel seriam feitas em aduelas de concreto pré-fabricado (Concrete Staves ), as quais nao poderiam receber furos passantes para fixação de qualquer estrutura metálica e que apresentavam grandes irregularidades na montagem dos seus 6 segmentos e possuiam instabilidade estrutural quanto a sua fixação na rocha cavada, instabilidade esta que permitia movimentos relativos entre os segmentos. Estes movimentos alem de acentuados entre eles, apresentavam vários pontos de inflexões da construção civil referentes ao eixo de centro do túnel e ao nível horizontal do piso, dificultando muito o alihamento e nivelamento do próprio Gasoduto.
A LIDERROLL desenvolveu e projetou todos os suportes côncavos para as paredes laterais de forma que a geometria dos mesmos imputassem forças convergentes contra a parede e obtivessem o maior atrito possivel para impedir o escorregamento da estrutura e permitir a aplicação de chumbadores pequenos que nao transfixassem o concreto e ao memso tempo anulassem os momentos de torção quando fossem exigidos pelos torques dos roletes motrizes. Chegamos ao desenho ideal após várias análises estruturais e simulações em modelos tridimensionais
Vencida esta etapa, a LIDERROLL passou para a 2ª fase da solução, que era calcular e avaliar todos os parâmentros de atrito para ver a capacidade de tração suficiente para vencer o peso da coluna, as forças resultantes da aclividade do túnel (3% de subida), a potência mecanica necessária para o deslocamento de toda a massa do gasoduto, a potencia elétrica necessária para mover todo o sistema, a compatibilidade com os espaços da movimentação dos trens, toda a logistica para instalação física, as analises de flexibilidade para verificar se a tubulação não iria pular de cima dos roletes motrizes e a avaliação dos esforços mecânicos no tubo e nos polímeros quando o duto estivesse em cantilever durante o tempo de seu deslocamento até chegar ao rolete motriz seguinte.
Resolvido e equacionado todos estes parâmetros físicos e já com a certeza da viabilidade mecânica de sua execução, passamos para fase seguinte do dimensionamento elétrico e sua alimentação no ambiente confinado com uma distância de 5.120 metros para alimentar 550 motores trifásicos de forma que não houvesse queda de tensão e ou riscos de queimar todos os motores. Para isso a LIDERROLL decidiu adotar a alimentação em Média tensão ( 13,8 Volts) e desta forma projetou e instalou uma usina de 2.0 Mva gerando em 480 V , elevando para 13,8 Kv e rebaixando dentro do túnel, a cada 500 metros, para 480 V de novo. Tudo controlado por uma sala de controles e supervisão acionada por uma mesa operadora com sistema de CFTV e fibra ótica na entrada do túnel onde os operadores poderiam controlar as operações de soldagem dos tubos e acionar a coluna com toda segurança.
Após todo o projeto e definição do sistema de geração de energia, da subestação elevatória de tensão, das redes de distribuição elétrica de baixa e média tensão, das conexões elétricas em cada motor dos roletes motrizes, foi necessário o desenvolvimento de um sistema de controle e supervisão visual da trajetória e comportamento que o gasoduto iria ter durante o seu trajeto de deslocamento horizontal, para que a tecnologia pudesse ser segura ao ponto de interrompermos as operações ao menor sinal de risco de colisão por desalinhamento e ou desnivelamento da coluna do duto. Contudo, por se tratar de uma distância de 5.100 metros e dentro de um túnel onde o sinal sofre reverberações e difração, tivemos que projetar e construir um sistema de cameras de supervisão com transmissão wireless para que o operador da cabine de controle pudesse ver em tempo real o comportamento do movimento do Gasoduto e se preciso, fazer a parada total da operação.
Mediante a possibilidade de termos que corrigir alguma direção do duto, potencializamos e projetamos o sistema para deslocar a coluna nos dois sentidos horizontal ( ida e vinda), ou seja, em regime normal a coluna do Gasoduto é lançada para dentro do túnel. Se houver a necessidade de troca de algum tubo ou reparo de alguma solda, o gasoduto tambem pode dar marcha à ré trazendo a coluna ou tubo para fora do tunel até o tubo desejado.
É importante registrar que toda concepção da nova metodologia e o desenvolvimento da tecnologia teria que ser à prova de erros, pois o túnel não teria uma outra saída do outro lado e como as pick-up entravam de frente e tinham que sair de marcha à ré sem possibilidades de manobras, corroborado ainda pelas grandes distâncias envolvidas, todo projeto foi simulado varias vezes, ou com a operação de protótipos construídos em tamanho real, ou utilizávamos a ferramenta de análise por elementos finitos. Todo ambiente de desenvolvimento e exaustivos testes foram criados em nossa fábrica com os vários protótipos produzidos em escala real. Em função disto Todas as fases de instalação e a operação na obra foram um sucesso.
Para registro: Sem contar o prazo da instalação elétrica e dos suportes com seus roletes (que foram instalados ao mesmo tempo em que a escavação civil do túnel estava sendo feita) a construção, soldagem e o lançamento horizontal de todo o Gasoduto de 28” X 0,625 X 5.100 metros, foi feita em 23 dias corridos, com soldagem pelo processo manual.
Esta nova tecnologia e metodologia construtiva de dutos criada e desenvolvida pela LIDERROLL, não foi uma simples adição ou aplicação de melhoria de qualquer processo já utilizado pelas construtoras mundiais ou o simples beneficiamento de novos aços em tecnologia já existente. Muito pelo contrário, a tecnolgia da LIDERROLL quebrou totalmente o paradigma construtivo da velha escola de dutos e substituiu com total eficiência as técnicas primitivas que primavam pelas atividades de transporte com caminhões e guindastes (sideboom) todos os tubos na operação de desfile por toda faixa do duto, alinhamento dos mesmos e avanço de todas as equipes de trabalho e suporte de logistica ao logo do trecho. Imaginem com fazer isto dentro de um ambiente confinado tipo túneis, valas e ou pântanos?
Com esta nova tecnologia, podem ser colocados pequenos e leves roletes motrizes a intervalos de 12 a 18 metros e com um sistema elétrico provisório, promover todo o lançamento da coluna dos gasodutos, oléodutos ou adutoras, 100% na posição HORIZONTAL e com isso obter menores prazos, menores custos e com as vantagens de que todas as atividades de soldagem, inspeção, fiscalização, reparos, alimentação de tubos, vestiários, refeitórios, escritórios, posto médico fiquem em um pipeshop fixo na boca do túnel, da vala ou da parte fixa do pântano, eliminando com isso os riscos de intoxicação por gases venenosos das soldas, má qualidade dos trabalhos e riscos de acidentes com a difícil e quase impossível remoção num caso de congestionamento do túnel por qualquer operação de carga e descarga utilizado pelo método antigo.
Esta nova tecnologia e metodologia construtiva da LIDERROLL promove, alem das vantagens já citadas, uma maior taxa de ocupação e aproveitamento dos túneis que é um investimento caro e de dificil construção, pois permite a aproximação de montagem entre os diversos dutos, uma vez que eles entram no sentido horizontal, e com isso pode-se instalar mais dutos dentro de um mesmo túnel.
Outro ponto de grande importância da nova tecnologia da LIDERROLL é que esta nova metodologia e equipamento desenvolvido (Rolete Motriz®), possui duas funções: A de dispositivo auxiliar de construção por lançamento com deslocamento 100% HORIZONTAL e quando o duto for colocado no seu lugar defnitivo, todo o sistema elétrico auxiliar é retirado e todos os roletes passam a funcionar como suporte definitivo do duto, permitindo sua acomodação sem oferecer riscos de amassamento do duto e proporcionando o grau de liberdade considerado pelas análises de flexibilidade da linha e impostos pelas forças de dilatação do aço dos tubos geradas pelo efeito delta de variação de temperatura, operação da linha e de seus fluidos.
Outro ponto de grande vantagem é que com esta tecnologia, os roletes motrizes podem assumir qualquer tamanho e geometrica específica e com pouco peso, logo os equipamentos utilizados para sua montagem e fixação também são de pequeno porte, permitindo com isso a construção de túneis de menores diâmetros e trazendo uma imensa redução do custo das obras civis e redução dos prazos de execução da construções destes túneis, sem com isso reduzir capacidade de linhas instaladas em seu interior. Abaixo temos um mini túnel de somente 60” de diâmetro externo; com 6 dutos instalados, sendo 2 dutos de 12”; 2 dutos de 8” e 2 dutos de 6”.
Em função disto, após o desenvolvimento desta tecnologia e a já consolidação, teste e aprovação pela Petrobras na adoção da construção de túneis para passagem de dutos; ficou comprovado que é mais viável utilizar faixas de dutos por dentro de túneis, eliminando com isso os impactos ambientais dos desmatamentos, operações de equipamentos pesados e os riscos geográficos na transposição de serras e montanhas, permitindo e incentivando o crescimento das malhas de dutos de todos os países, de forma limpa, segura, rápida e eficaz.